Acero inoxidable 904L 1.4539
Solicitud
Planta química, refinería de petróleo, plantas petroquímicas, tanques de blanqueo para la industria papelera, plantas de desulfuración de gases de combustión, aplicación en agua de mar, ácido sulfúrico y fosfórico.Gracias al bajo contenido de C, la resistencia a la corrosión intergranular también está garantizada en estado soldado.
Composiciones químicas
Elemento | % Presente (en forma de producto) |
Carbono (C) | 0,02 |
Silicio (Si) | 0,70 |
Manganeso (Mn) | 2.00 |
Fósforo (P) | 0,03 |
Azufre (S) | 0,01 |
Cromo (Cr) | 19.00 - 21.00 |
Níquel (Ni) | 24.00 - 26.00 |
Nitrógeno (N) | 0,15 |
Molibdeno (Mo) | 4.00 - 5.00 |
Cobre (Cu) | 1.20 - 2.00 |
Hierro (Fe) | Balance |
Propiedades mecánicas
Propiedades mecánicas (a temperatura ambiente en estado recocido)
Formulario de producto | |||||||
C | H | P | L | L | DOS/TS | ||
Espesor (mm) Máx. | 8.0 | 13.5 | 75 | 160 | 2502) | 60 | |
Fuerza de producción | Rp0,2N/mm2 | 2403) | 2203) | 2203) | 2304) | 2305) | 2306) |
Rp1,0N/mm2 | 2703) | 2603) | 2603) | 2603) | 2603) | 2503) | |
Resistencia a la tracción | Sala N/mm2 | 530 - 7303) | 530 - 7303) | 520 - 7203) | 530 - 7304) | 530 - 7305) | 520 - 7206) |
Elongación mín.en % | Jmín (longitudinal) | - | 100 | 100 | 100 | - | 120 |
Jmin (Transversal) | - | 60 | 60 | - | 60 | 90 |
Dato de referencia
Densidad a 20°C kg/m3 | 8.0 | |
Conductividad térmica W/m K a | 20ºC | 12 |
Módulo de elasticidad kN/mm2 en | 20ºC | 195 |
200ºC | 182 | |
400°C | 166 | |
500°C | 158 | |
Capacidad Térmica Específica a 20°CJ/kg K | 450 | |
Resistividad eléctrica a 20°C Ω mm2/m | 1.0 |
Procesamiento / Soldadura
Los procesos de soldadura estándar para este grado de acero son:
- Soldadura TIG
- Alambre sólido para soldadura MAG
- Soldadura por arco (E)
- Soldadura por láser
- Soldadura por arco sumergido (SAW)
A la hora de elegir el metal de aportación también hay que tener en cuenta la tensión de corrosión.Puede ser necesario el uso de un metal de aportación de mayor aleación debido a la estructura fundida del metal de soldadura.Para este acero no es necesario precalentar.Normalmente no es habitual un tratamiento térmico después de la soldadura.Los aceros austeníticos sólo tienen el 30% de la conductividad térmica de los aceros no aleados.Su punto de fusión es más bajo que el del acero no aleado, por lo que los aceros austeníticos deben soldarse con un menor aporte de calor que los aceros no aleados.Para evitar el sobrecalentamiento o el quemado de láminas más delgadas, se debe aplicar una velocidad de soldadura más alta.Las placas de respaldo de cobre para un rechazo más rápido del calor son funcionales, mientras que, para evitar grietas en el metal de soldadura, no se permite fusionar la superficie de la placa de respaldo de cobre.Este acero tiene un coeficiente de expansión térmica mucho más alto que el acero no aleado.Debido a una peor conductividad térmica, es de esperar una mayor distorsión.Al soldar 1.4539 se deben respetar especialmente todos los procedimientos que evitan esta distorsión (p. ej. soldadura en secuencia inversa, soldadura alternativa en lados opuestos con soldadura a tope en doble V, asignación de dos soldadores cuando los componentes son correspondientemente grandes).Para espesores de producto superiores a 12 mm, se debe preferir la soldadura a tope en doble V en lugar de una soldadura a tope en V simple.El ángulo incluido debe ser de 60° - 70°, cuando se utiliza soldadura MIG unos 50° son suficientes.Se debe evitar la acumulación de cordones de soldadura.Los puntos de soldadura deben colocarse a distancias relativamente más cortas entre sí (mucho más cortas que las de los aceros no aleados) para evitar fuertes deformaciones, encogimientos o descamaciones de los puntos de soldadura.Las tachuelas deben pulirse posteriormente o al menos estar libres de grietas.1.4539 En relación con el metal de soldadura austenítico y un aporte de calor demasiado alto, existe la tendencia a formar grietas por calor.La adicción a las grietas por calor puede limitarse si el metal de soldadura tiene un menor contenido de ferrita (ferrita delta).Contenidos de ferrita de hasta el 10 % tienen un efecto favorable y, en general, no afectan a la resistencia a la corrosión.Se debe soldar la capa más fina posible (técnica de cordón continuo), ya que una mayor velocidad de enfriamiento disminuye la adicción a las grietas calientes.También durante la soldadura se debe aspirar a un enfriamiento rápido, para evitar la vulnerabilidad a la corrosión intergranular y la fragilización.1.4539 es muy adecuado para la soldadura por rayo láser (soldadura A según el boletín DVS 3203, parte 3).Con un ancho de ranura de soldadura inferior a 0,3 mm o 0,1 mm de espesor del producto, no es necesario el uso de metales de aportación.Para ranuras de soldadura más grandes se puede utilizar un metal de aportación similar.Al evitar la oxidación dentro de la superficie de la costura mediante soldadura por rayo láser mediante soldadura de revés, por ejemplo con helio como gas inerte, la costura de soldadura es tan resistente a la corrosión como el metal base.Al elegir el proceso adecuado no existe peligro de rotura en caliente para la costura de soldadura.1.4539 también es adecuado para corte por fusión con haz láser con nitrógeno o corte con llama con oxígeno.Los bordes cortados sólo tienen pequeñas zonas afectadas por el calor y generalmente están libres de microfisuras y, por lo tanto, son bien moldeables.Al elegir un proceso aplicable, los bordes cortados por fusión se pueden convertir directamente.Especialmente, se pueden soldar sin necesidad de preparación adicional.Durante el procesamiento sólo se permiten herramientas de acero inoxidable como cepillos de acero, picos neumáticos, etc., para no poner en peligro la pasivación.Se debe omitir marcar dentro de la zona de la costura de soldadura con pernos oleaginosos o crayones indicadores de temperatura.La alta resistencia a la corrosión de este acero inoxidable se basa en la formación de una capa pasiva homogénea y compacta en la superficie.Para no destruir la capa pasiva deben eliminarse los colores de recocido, las incrustaciones, los residuos de escoria, los restos de hierro, las salpicaduras y similares.Para la limpieza de la superficie se pueden utilizar los procesos de cepillado, esmerilado, decapado o granallado (arena de sílice sin hierro o esferas de vidrio).Para el cepillado sólo se pueden utilizar cepillos de acero inoxidable.El decapado de la zona de la costura previamente cepillada se realiza mediante inmersión y pulverización, sin embargo, a menudo se utilizan pastas o soluciones de decapado.Después del decapado se debe enjuagar cuidadosamente con agua.
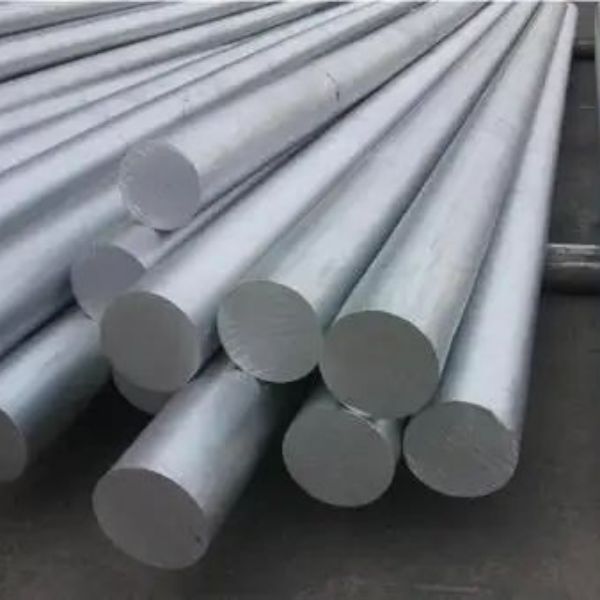
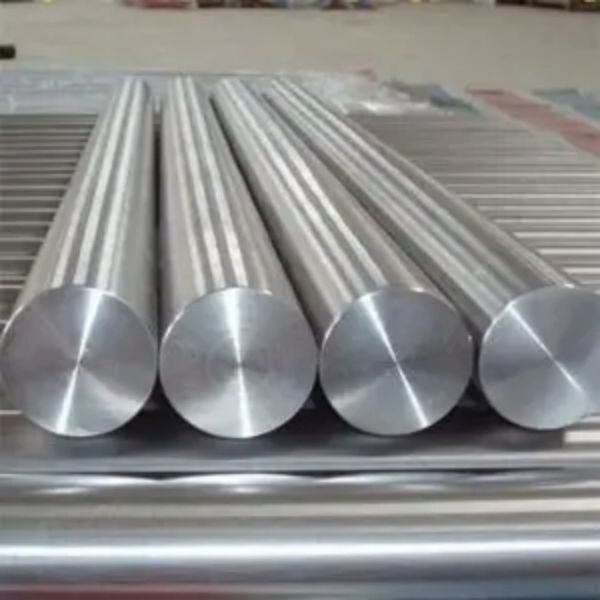
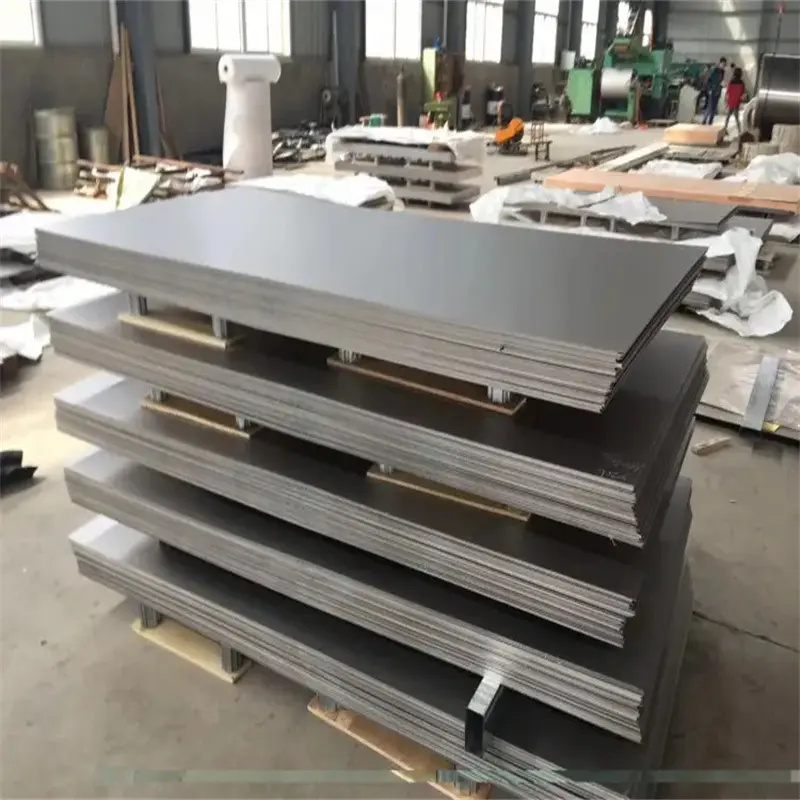
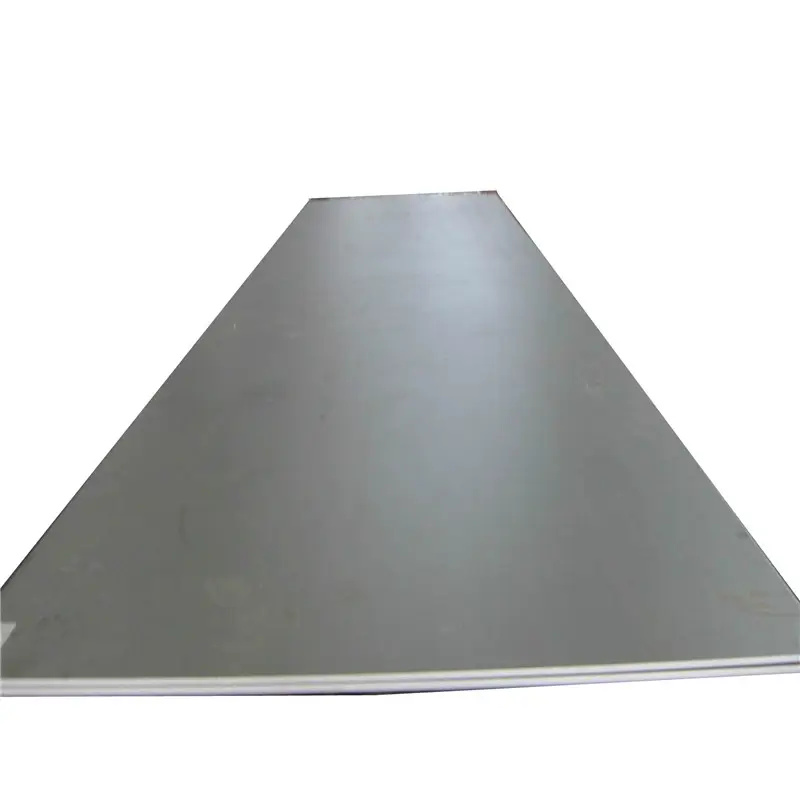